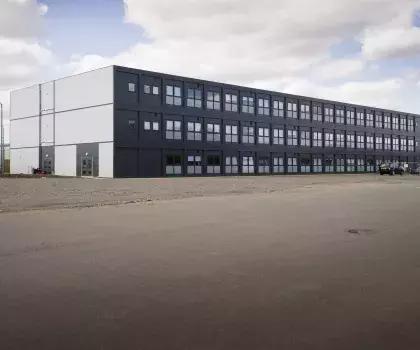
Modular buildings: Responding to change
Manufacturers often face challenges when it comes to accommodating changes in their workforce or office space needs. Whether it's the influx of seasonal workers during busy periods, the need to refurbish permanent offices, or the rapid growth of the business, finding a flexible and cost-effective solution is crucial.
Here, [Spokesperson] at Algeco looks at why more manufacturers are opting for temporary modular buildings for hire to address their business needs.
Temporary modular buildings provide manufacturers with several key benefits. Firstly, they offer flexibility, allowing manufacturing and industrial businesses to quickly scale up or down their workforce welfare requirements based on demand. This is particularly important for those that experience seasonal fluctuations in their workforce. By utilising temporary modular buildings for hire, manufacturers can easily accommodate the additional staff during peak seasons without the need for long-term commitments or costly expansions associated with permanent builds.
Many manufacturers also find that temporary modular buildings are more cost-effective, especially because hiring temporary buildings doesn’t require a large capital outlay like with permanent structures. This cost savings can be significant, especially for manufacturers that need to allocate their budget strategically.
What really stands out, though, is that temporary modular buildings are quick to install. Unlike traditional construction methods that can take months or even years, modular buildings can be set up in a matter of weeks, whilst turnkey solutions mean they are ready for workers from day one. This rapid installation allows manufacturers to respond swiftly to changing business needs without causing significant disruptions to their operations or cashflow.
Climate control delivers outstanding energy savings and comforts, meaning that modular buildings often perform as good or better than a permanent build, and are certainly better for the environment. Our circular ‘Loops within Loops’ model is one where the majority of the material has an ongoing life, where materials are retained in use at their highest value for as long as possible and then reused or recycled, leaving minimal residual waste. That means once the building modules reach the end of the hire period, we refurbish them and send them out to the next customers.
Responding to business demands
Manufacturers often experience fluctuations in their workforce, particularly during busy seasons. Hiring seasonal workers can help meet this increased demand, but it can present a challenge when it comes to providing suitable accommodation, which is why more are opting for temporary modular buildings.
These buildings can be customised to provide comfortable office and welfare spaces, or even create living spaces for workers on remote projects, including bedrooms, common areas, and kitchen facilities. By providing temporary accommodation on-site, manufacturers can ensure that their seasonal workers have a convenient and comfortable place to stay, improving their overall well-being and productivity. Done correctly, and it can help attract and retain a more skilled workforce.
Refurbishing existing premises
Office refurbishments are a common occurrence for manufacturers as they strive to create modern and functional workspaces. However, renovating existing offices can be time-consuming and disruptive to daily operations, whereas temporary modular buildings offer a convenient alternative during the refurbishment process.
They allow manufacturers to set up temporary modular buildings on-site to serve as office spaces while the renovations take place. These buildings can be fully equipped with workstations, meeting rooms, and other necessary amenities allowing employees to continue their work without major interruptions during the refurbishment period.
Temporary modular buildings also provide manufacturers with the flexibility to customise the layout and design of the office space. This allows businesses to create tailored work environments that meet their specific needs and enhance employee satisfaction and productivity. They also have the advantage of scalability; As business needs change, manufacturers can easily add or remove modular units to match their evolving requirements. This flexibility allows businesses to adapt to market demands and optimise their operations efficiently.
Choosing a Temporary Modular Building Provider
Once you’ve identified the need for a modular building, start by outlining your requirements. What will it be used for? How many people do you need to accommodate and here, Health & Safety Executive (HSE) guidelines recommend 11 cubic metres per person. What types of rooms and how many of each are required? Again, HSE guidelines state that two toilets and two handbasins are needed for every 25 people.
The type of welfare facilities required will vary depending on the size and nature of the space. However, as a minimum, we recommend you include the following:
- Toilets: should be connected to the mains plumbing if possible, but inbuilt water supplies are acceptable. Toilets should be well-maintained, ventilated, and well-lit.
- Drinking water: Workers should have access to clean drinking water at all times. This can be provided through bottled water, coolers, or taps that are connected to the mains supply.
- Washing facilities: Workers should have access to washing facilities, including sinks with running water, soap, and towels. Showers may be needed, depending on the nature of the work being carried out.
- Rest rooms: Workers should have a place to rest and relax during breaks. This could be a dedicated rest room or simply a shaded area with seating.
- Changing rooms: Workers who need to change into protective clothing should have access to clean, well-ventilated changing rooms.
However, when setting out your requirements, it’s important to think beyond the basics and consider your employees’ social, religious and personal needs too. We’re seeing increased demand for facilities such as prayer rooms, smoking shelters, segregated bathrooms and quiet breakout spaces.
Fire regulations will also inform the design and fit-out of the building. A full fire safety risk assessment must be carried out, and as part of your fire safety strategy, you need to make sure that you have the correct type and quantity of fire safety equipment to meet the requirements of your risk assessment. We recommend obtaining professional fire safety advice from your modular building provider.
When your designs are finalised, you’ll need to apply for planning permission. Unless they’re on-site for less than 28 days, all modular buildings need planning permission (except for construction site accommodation), and the process usually takes 4-8 weeks.
A plug ‘n Play solution
Modular buildings for hire are a sustainable and cost-effective way to provide flexible workspaces and facilities for staff. That makes them highly suited to addressing the challenges around seasonal workers, office refurbishments, and business growth, amongst others.
Ultimately, by helping you to meet your business needs it allows you to optimise operations and create a conducive work environment for employees. As such, temporary modular buildings are an effective way forward for manufacturers looking to adapt quickly and efficiently to change.
To find out more about Algeco temporary buildings for hire, visit: https://www.algeco.co.uk/temporary